Tailor-made program matching the product
A powdered seasonings manufacturer, N Corporation, told us, “Without human labor, we want to operate our plant for 24 hours continuously without halting manufacturing.” So we proposed and supplied a centrifuge enabling fully automated manufacturing.
As a result of using our centrifuge, operation from raw material input to discharge and cleaning of the machine interior was automated, leading to labor savings and increased manufacturing efficiency.
Key Points – In-depth hearings and meetings
We proposed the optimal specification after in-depth meetings
We conducted tests with a test machine to determine the viscosity and filtration characteristics of the products that the customer wanted to filter and process.
We investigated the optimal machine specification for the customer product with the help of mechanical technology members and electrical program technology members, and held meetings about the movement of the centrifuge and the time for each process.
We created an operating pattern that matched the product, and created a tailor-made, optimal program based on customer hearings.
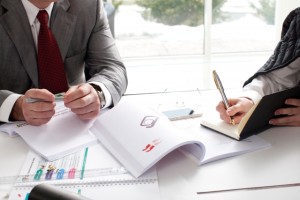
Meeting with expert staff from each section
A variety of recipes
Since multiple products are switched over a fixed period, and 1 centrifuge carries out water removal processing of multiple products, 12 types of recipes were created.
The products are processed by programs with 12 patterns.
The recipes can be added to at any time even after installation of the centrifuge.
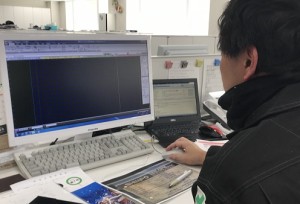
The electrical program creates recipes
Automation of product insertion
Using an over-feed prevention device, the amount of product inserted into the centrifuge is optimized, and the insertion automatically stops, and the filtration and water removal process starts.
The optimal g (centrifugal force) for the process is controlled automatically
Since variable speed control is effected that can freely alter the rotation speed, filtration and water removal processing at the optimal g (centrifugal force) for the product is possible.
Peace of mind even in case of emergency
Since the machine is equipped with interlockings, abnormal vibration detection equipment, a rotation speed compensation system, and so on, the safety equipment automatically operates in the event of an emergency.
Automation of product discharge
After completion of the filtration and water removal process and the crystal washing process, the crystals are automatically scraped off and discharged outside the centrifuge.
Prior to the automation support, the operator crushed the hard crystals with a scoop, and scooped them out of the centrifuge.
The automatic residual crystal detachment device, the Screw
Automation of cleaning of the centrifuge interior after manufacture of the product
The machine interior cleaning device enables automatic cleaning of the centrifuge interior.
Company supplied
The powdered seasonings manufacturer, N Corporation
Centrifuge supplied
For any questions or inquiries regarding centrifuges, feel free to contact Matsumoto Machine Sales, the sales arm of the pioneering centrifuge manufacturer.